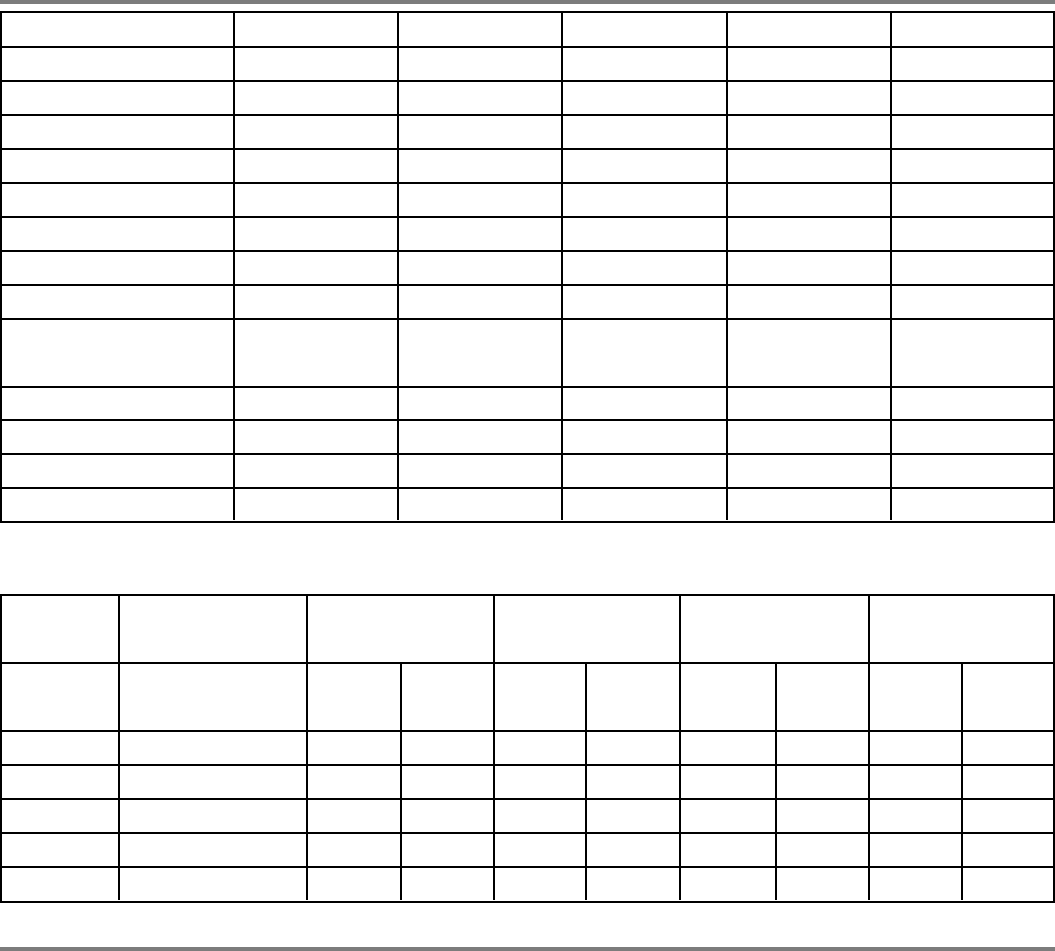
B. ICE BIN LEVEL SENSOR
The ice bin level temperature sensor, secured to one of the storage bin walls, stops the operation of the entire ice maker at the end of the defrost
cycle when its sensing probe (in contact with the stored ice) reaches the temperature of +2˚C (35˚F) lighting up, in the meantime, the third
RED
LED.
Once the ice is removed from the sensing probe, its temperature progressively rises up and as it reaches the value of +4.5˚C (40˚F) the ice bin
level temperature sensor transmits a low voltage current flow to the P.C. BOARD to restart the operation of the unit.
NOTE: The ice maker, after the interruption of its operation due to the ice level control cut-out, always restarts from the beginning of the freezing
cycle.
By changing the combination of the DIP SWITCH Keys numbers 8 and 9 it is possible to change the range of the ice level control temperature
sensor. This is shown in table D, keeping its cut out temperature always at +2˚C (35˚F).
C. P.C. BOARD (Data processor)
The P.C. BOARD, fitted in its plastic box located in the front of the unit, consists of two separated printed circuits one at high and the other at
low voltage integrated with a program selector; of six aligned
LEDS monitoring to the service engineer the operation of the machine; of one
DIP SWITCH with ten keys; of input terminals for the leads of the two sensor probes and of input and output terminals for the leads of the ice
maker electrical wires.
The P.C. BOARD is the brain of the system and it processes, through its microprocessor, the signals received from the two sensors in order to
control the operation of the different electrical components of the ice maker (compressor, water pump, solenoid valves, etc.).
By turning the program selector it is possible to put the unit in the following different situations:
CLEANING/RINSING The water pump is the only electrical component in operation and it must be used during the cleaning or the rinsing
procedure of the water system of ice machine.
STAND BY The unit remains under electrical power but OUT of operation. It can be used by the service engineer in order to stop the unit during
the service and inspection operations.
IN OPERATION The unit is running through the freezing and defrost cycles stopping automatically only at full bin situation.
RE-SET To be selected to resume the unit operation when the ice maker shuts off due to the intervention of the security of the P.C. BOARD in
relation to exceeding the time of freezing cycle portion T1 and T2.
The six LEDS (not visible through the panel) placed in a vertical row in the front of the P.C. BOARD, monitor, from the top to the bottom, the
following situations:
GREEN LIGHT Unit under electrical power
RED LIGHT Unit shut-off due to P.C. BOARD security (T1 >15’ or T2>45’)
RED LIGHT Unit shut-off at full storage bin
RED LIGHT Evaporator sensor at -13˚C (85˚F) or -16˚C (3˚F)
RED LIGHT Evaporator sensor at 0˚C (35˚F)
RED LIGHT Unit in freezing cycle mode
The microprocessor of the P.C. BOARD has also the important function to establish the length of the defrost cycle Ts in relation with the duration
of the second phase of the freezing cycle or time T2 as shown in Table B. Page 12.
6.5 Dip Switch
The P.C. BOARD which controls the entire operation of the ice maker, has a DIP SWITCH with ten switching keys which allow set up of
the microprocessor program in order to extend or to shorten the length of freezing cycle in relation to the different models and versions of ice
machines and to modify the sensing range of the ice bin level temperature sensor.
The 1st DIP SWITCH key is used to supply power to the water pump during the first 15-20 seconds of the defrost cycle to pump out all remaining
water from the sump tank in the unit along with the water drain valve.
The 2nd DIP SWITCH key allows a rapid check up (auto-diagnosis) to be made of the P.C. BOARD output connections (compressor, water
pump, fan motor, water inlet and hot gas solenoid valves) energising them in rapid sequence (2 seconds) one by one.
DURING THE AUTOMATIC OPERATION OF THE ICE MAKER THIS KEY MUST BE SET IN OFF POSITION.
ATTENTION The check up of the P.C. BOARD output must be performed in a very short time in order to avoid frequent start and stop
(every few seconds) of the electrical components which may damage them - especially the compressor.
The setting of the DIP SWITCH keys 3, 4, 5, 6 and 7 determines the length of the 3rd phase of freezing cycle (controlled by the electronic
timer) as detailed in Table B. Page 12.
The DIP SWITCH keys 8 and 9 setting determines the range between cut in and cut out temperature of the ice bin level temperature sensor
as specified in Table D. Page 12.
The 10th DIP SWITCH key is used to change the setting of the evaporator temperature sensor from -13˚C (8.5˚F) - OFF position
(20,30,40
and 60 to -16˚C (3˚F) - ON position on model 85.
11
9. Technical Specification - R134A Machines
MODEL FCI 20 FCI 30 FCI 40 FCI 60 FCI 85
Output – kg/24hr. 18 26 34 57 76
Ice prod. per cycle 0.28kg 0.42kg 0.42kg 0.86kg 0.86kg
Freeze time cycle 19.5 min 21.2 min 16 min 19.5 min 14.5 min
Cubes per cycle 16 24 24 48 48
Bin capacity kg 6.5 15 15 27 27
Electrical Supply 230/1/50 Hz 230/1/50 Hz 230/1/50 Hz 230/1/50 Hz 230/1/50 Hz
Amp start / run 11amp/2amp 11amp/2.2amp 17amp/3.3amp 19amp/4.1amp 26amp/5.5amp
Fuse rating 10A 10A 10A 10A 16A
Watts consumption
320 340 450 630 780
(30°C ambient)
Water consumption 7.5 litre per hr 5.6 litre per hr 6.2 litre per hr 11.0 litre per hr 14.5 litre per hr
Min evap Temp °C -26°C -26°C -26°C -26°C -26°C
Heat rejection watts 0.540 0.580 0.850 1.1 1.4
Noise level dBA < 70 dB < 70 dB < 70 dB < 70 dB < 70 dB
Model Refrig. & Charge
Start Cycle End Cycle Start Cycle End Cycle
21°C amb/15°C w 21°C amb/15°C w 32°C amb/15°C w 32°C amb/15°C w
Cond Evap Cond Evap Cond Evap Cond Evap
(bar) (°C) (bar) (°C) (bar) (°C) (bar) (°C)
FCI 20 R134A 0.250kg 10 -7 6.5 -27 13 -5 8 -26
FCI 30 R134A 0.230kg 12 -5 7 -26 16.5 -2 9.5 -24
FCI 40 R134A 0.320kg 11 -9 8.5 -26 14 -6 9.5 -24
FCI 60 R134A 0.450kg 11 -8 8.5 -27 14 -6 9 -25
FCI 85 R134A 0.540kg 11 -8 8 -26 15 -6 9.5 -24
R134A Ice Machines Technical Data
(air cooled)
10. Operating Instructions - FCI 40 - 60 - 85 Only (For FCI 20-30 see previous section)
10.1 Start Up
After having correctly installed the ice maker and completed the plumbing and electrical connections, perform the following “Start-up”
procedure.
A. Remove the unit front panel and locate the control box.
B. Through the control box cover locate the grooved head (similar to a fillister screw head) of the electronic program selector.
With the help of a regular screwdriver turn the selector head in the OPERATION position. (The screwdriver bit must fit the head slot end to end,
this to avoid damage to the selector head slot).
C. Give power to the unit to start it up by switching ‘ON’ the power line main disconnect switch.
NOTE: Every time the unit returns under power, after having been switched off, both the water inlet valve and the hot gas valve get energized
for a period of 5 minutes, thus to admit new water to the machine sump reservoir to fill it up and, eventually, to wash-off any dirt that can have
deposited in it during the unit off period (Fig.1).
D. During the water filling operation, check to see that the incoming water dribbles through the evaporator platen dribbler holes, down into the
sump reservoir to fill it up and also that the incoming surplus of water flows out through the overflow pipe into the drain line.
During the water filling phase the components energized are:
THE WATER INLET SOLENOID VALVE
THE HOT GAS SOLENOID VALVE
THE WATER DRAIN SOLENOID VALVE
(On request)
NOTE: If in the 5 minutes length of the water filling phase the machine sump reservoir does not get filled with water up to the rim of the overflow
pipe, it is advisable to check:
1. The water pressure of the water supply line that must be at least 1 bar (14 psig) Minimum (Max 5 Bar-70 psig).
2. The filtering device installed in the water line that may reduce the water pressure below the Minimum value of 1 bar (14 psig).
3. Any clogging situation in the water circuit like the inlet water strainer and/or the flow control.
14