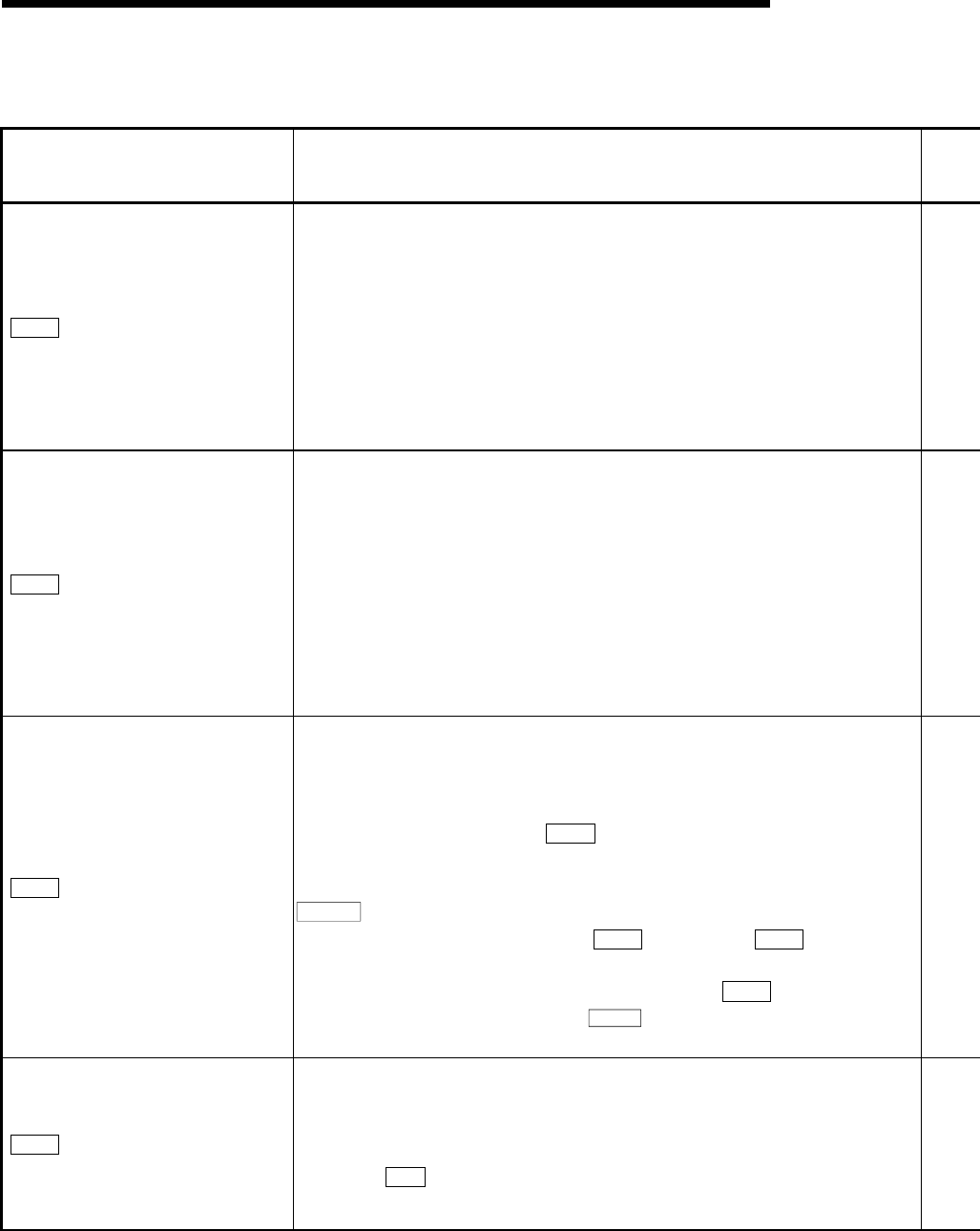
5 - 128
MELSEC-Q
5 DATA USED FOR POSITIONING CONTROL
5.6.2 Axis monitor data
Storage item Storage details
Md.20
Current feed value
The currently commanded address is stored.
(Different from the actual motor position during operation)
The current position address is stored.
If "degree" is selected as the unit, the addresses will have a ring structure for values
between 0 and 359.99999 degrees.
•
Update timing : 1.7ms
•
The OP address is stored when the machine OPR is completed.
•
When the current value is changed with the current value changing function, the
changed value is stored.
Md.21
Machine feed value
The address of the current position according to the machine coordinates will be
stored. (Different from the actual motor position during operation)
Note that the current value changing function will not change the machine feed
value.
Under the speed control mode, the machine feed value is constantly updated
always, irrespective of the parameter setting.
The value will not be cleared to "0" at the beginning of fixed-feed control.
Even if "degree" is selected as the unit, the addresses will not have a ring structure
for values between 0 and 359.99999 degrees.
•
Machine coordinates: Characteristic coordinates determined with machine
•
Update timing: 56.8ms
Md.22
Feedrate
The speed of the operating workpiece is stored. (May be different from the actual
motor speed during operation)
•
During interpolation operation, the speed is stored in the following manner.
Reference axis : Composite speed or reference axis speed
(Set with
Pr.20
)
Interpolation axis : 0
•
Update timing: 56.8ms
POINT
In case of the single axis operation,
Md.22
Feedrate and
Md.28
Axis feedrate
are identical.
In the composite mode of the interpolation operation,
Md.22
Feedrate is a
speed in a composite direction and Md.28
Axis feedrate is that in each axial
direction.
Md.23
Axis error No.
When an axis error is detected, the error code corresponding to the error details is
stored.
•
The latest error code is always stored.
(When a new axis error occurs, the error code is overwritten.)
•
When "
Cd.5
Axis error reset" (axis control data) turns ON, the axis error No. is
cleared (set to 0).