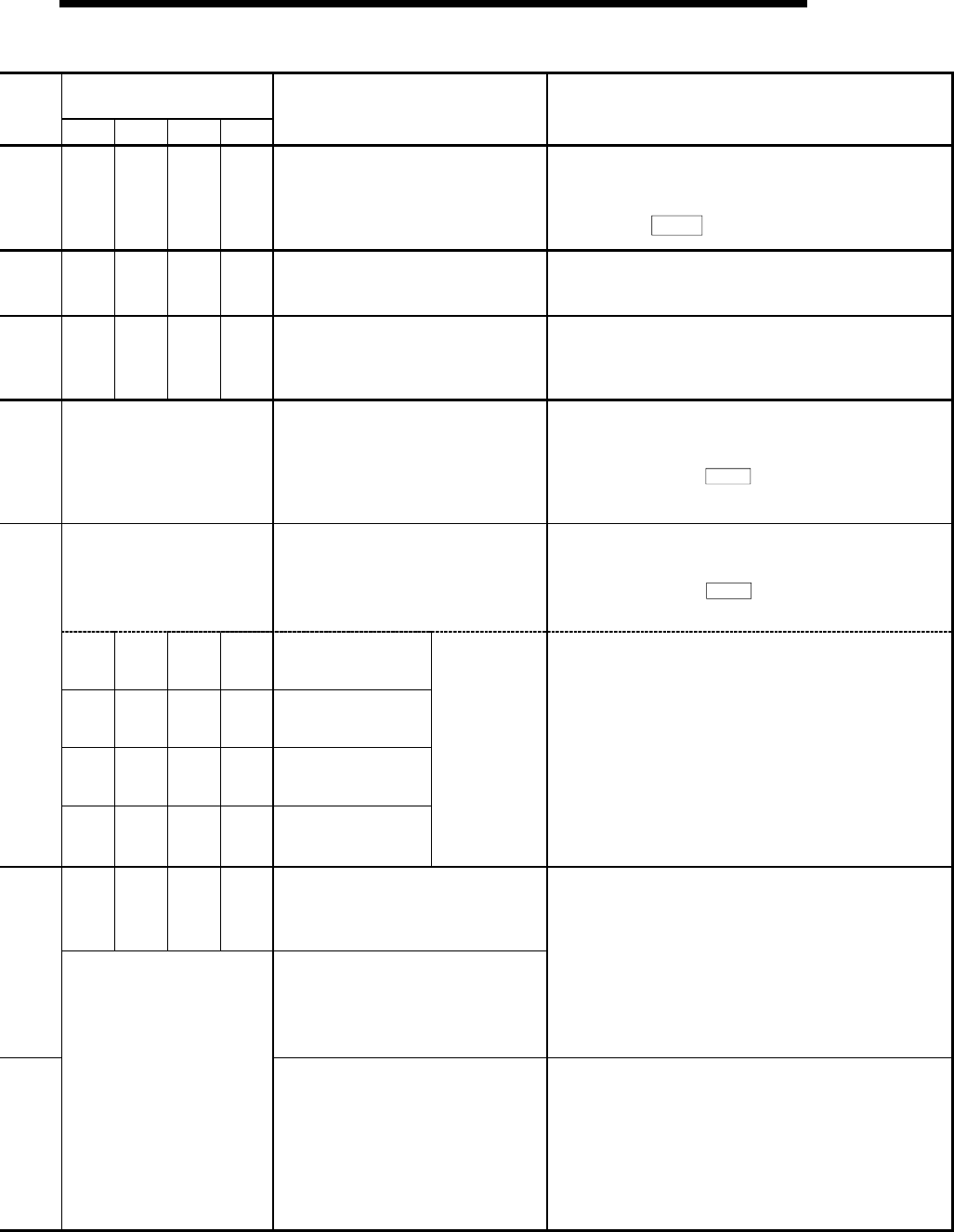
15 - 11
MELSEC-Q
15 TROUBLESHOOTING
Related buffer memory
address
Axis 1 Axis 2 Axis 3 Axis 4
Set range
(Setting with PLC program)
Remedy
32 182 332 482
<External input signal selection>
0,1
When the count method 1) or 2) – machine home
position return (OPR) is used, the near-point dog is set
to "0: External input signal of QD75MH". (Refer to
Section 5.2.3
Pr.80
)
1518
1519
1618
1619
1718
1719
1818
1819
<JOG speed>
1 to 50000000 [PLS/s]
1 to 2000000000 [mm/min or others]
Bring JOG speed into the setting range.
(Refer to Section 11.2)
1517 1617 1717 1817
<Inching movement amount>
0 to 65535
Reduce the inching movement amount.
(Refer to Section 11.3)
Refer to Section 5.4
"List of block start data"
<Condition data No.>
1 to 10
Review the condition data No.
(Refer to Section 5.4
Da.14
)
Refer to Section 5.5
"List of condition data"
<Condition operators>
Axis designation:
10
H
, 20
H
, 30
H
, 40
H
, 50
H
,
60
H
, 70
H
, 80
H
, 90
H
, A0
H
,
B0
H
, C0
H
, D0
H
, E0
H
Review the simultaneous start axis start data No. .
(Refer to Section 5.5
Da.16
)
1540 1640 1740 1840 Axis 1 start data No.
1541 1641 1741 1841 Axis 2 start data No.
1542 1642 1742 1842 Axis 3 start data No.
1543 1643 1743 1843 Axis 4 start data No.
Simultaneous
start axis start
data No.
0 to 600
Review the simultaneous start axis start data No. to
correct value.
(Refer to Section 10.5)
1500 1600 1700 1800
<Positioning start No.>
1 to 600,
7000 to 7004,
9001 to 9004
<JUMP destination>
1 to 600
Review the positioning start No., positioning start data
(in block start), and positioning data (in JUMP
instruction) to correct value.
Refer to Section 5.3
"List of positioning data"
<Command speed>
1 to 50000000 [PLS/s]
1 to 2000000000 [mm/min or others]
Review the positioning data to correct value.