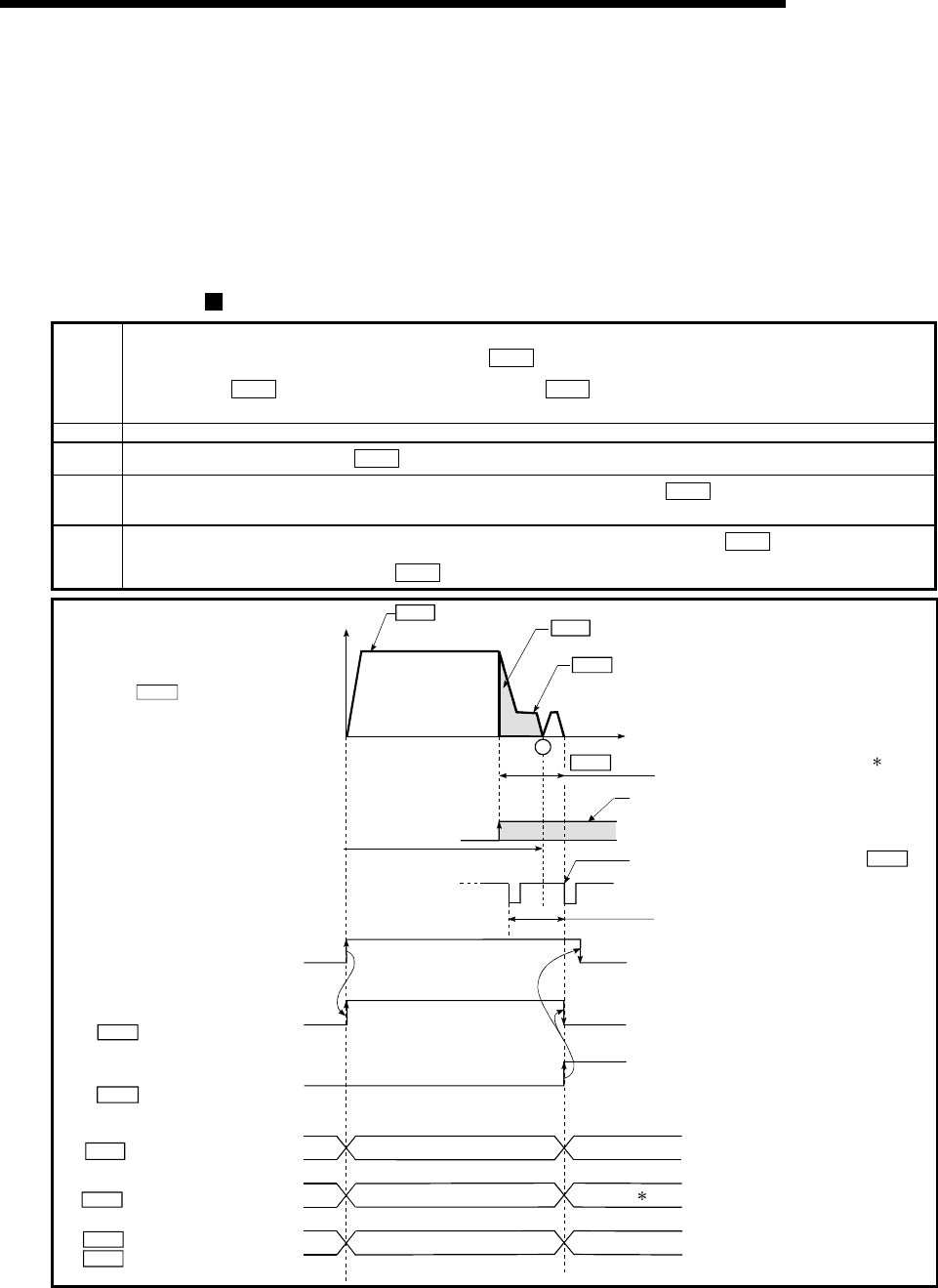
8 - 9
MELSEC-Q
8 OPR CONTROL
8.2.4 OPR method (2): Count method 1)
The following shows an operation outline of the "count method 1)" OPR method.
In the "count method 1)" OPR, the following can be performed:
•
Machine OPR on near-point dog
•
Second machine OPR after completion of first machine OPR
Near-point dog is used to the external device connector of the QD75MH. The "Illegal
near-point dog signal" (error code : 220) will occur if you used external input signal of
the servo amplifier.
Operation chart
1)
The machine OPR is started.
(The machine begins the acceleration designated in "
Pr.51
OPR acceleration time selection", in the direction
designated in "
Pr.44
OPR direction". It then moves at the "
Pr.46
OPR speed" when the acceleration is
completed.)
2) The machine begins decelerating when the near-point dog ON is detected.
3)
The machine decelerates to the "
Pr.47
Creep speed", and subsequently moves at that speed.
4)
The machine stops after the workpiece has been moved the amount set in the "
Pr.50
Setting for the movement
amount after near-point dog ON" after the near-point dog turned ON. It then restarts and stops at the first zero point.
5)
After a "deviation counter clear output" is output to the drive unit, the OPR complete flag
Md.31
Status: b4) turns from
OFF to ON, and the OPR request flag (
Md.31
Status: b3) turns from ON to OFF.
t
ON
OFF
ON(1)
OFF(0)
OFF(0)
ON(1)
0
V
ON
Pr. 47 Creep speed
Pr. 46 OPR speed
Pr. 50 Setting for the movement amount
after near-point dog ON
Md.34 Movement amount after near-point dog ON
Zero signal
Near-point dog OFF
Leave sufficient distance from the zero point
position to the near-point dog OFF
OPR start
Standing by
In OPR
Md.26 Axis operation status
Inconsistent
Value the machine moved is stored
OP address
Value of 1.
Standing by
Inconsistent
OPR request flag
[ Md.31 Status : b3]
OPR complete flag
[ Md.31 Status : b4]
Md.21 Machine feed value
Md.34 Movement amount
after near-point dog ON
Md.20 Current feed value
1
Adjust the setting for the movement amount after
near-point dog ON to be as near as possible to
the center of the zero signal HIGH.
If the setting for the movement amount after
near-point dog ON falls within the zero signal,
there may be produced an error of one servo
motor rotation in the OPR stop position.
One servo motor rotation
First zero signal after moving a set to " Pr. 50
Setting for the movement amount after near-
point dog ON.
A
POINT
After the home position return
(OPR) has been started, the
zero point of the encoder must
be passed at least once before
point A is reached.
Fig. 8.5 Count method1) machine OPR