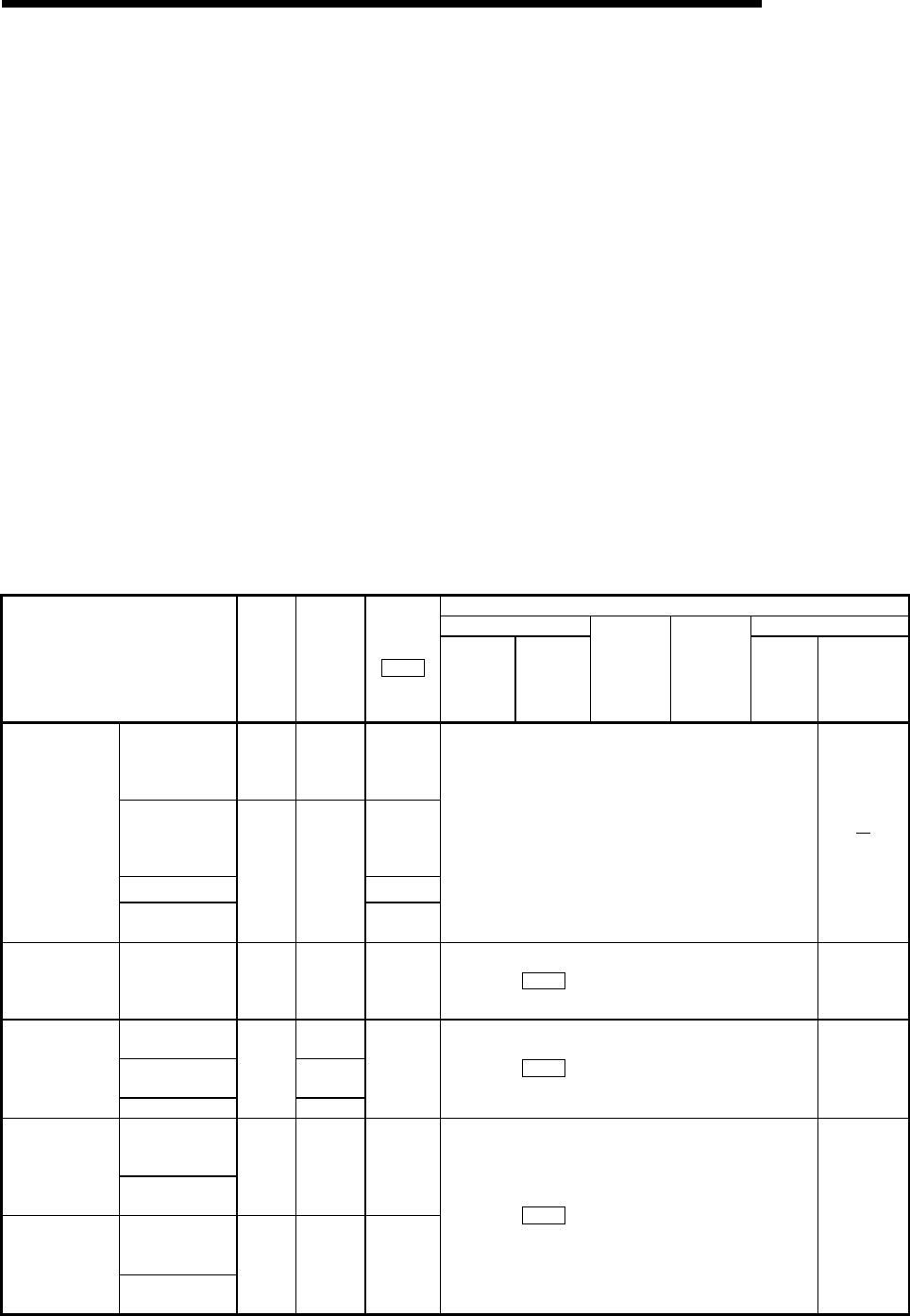
6 - 69
MELSEC-Q
6 PLC PROGRAM USED FOR POSITIONING CONTROL
6.5.6 Stop program
The axis stop signal [Y4, Y5, Y6, Y7] or a stop signal from an external device is used to
stop the control.
Create a program to turn ON the axis stop signal [Y4, Y5, Y6, Y7] as the stop program.
The process for stopping control is explained below.
Each control is stopped in the following cases.
(1) When each control is completed normally.
(2) When the Servo READY signal is turned OFF.
(3) When a PLC CPU error occurs.
(4) When the PLC READY signal is turned OFF.
(5) When an error occurs in QD75MH.
(6) When control is intentionally stopped
(Stop signal from PLC CPU turned ON, stop signal from peripheral devices)
The stop process for the above cases is shown below.
(Excluding item (1) above "When each control is completed normally".)
[1] Stop process
Stop process
OPR control Manual control
Stop cause Stop axis
M code
ON signal
after stop
Axis
operation
status
(
Md.26
)
after
stopping
Machine
OPR
control
Fast OPR
control
Major
positioning
control
High-level
positioning
control
JOG/
Inching
operation
Manual pulse
generator
operation
"Forced stop input
signal from an
external device"
OFF
All axes No change Servo OFF
Servo READY OFF
• Servo amplifier
power supply
OFF
Servo
amplifier
disconnected
• Servo alarm During error
Forced stop
• Forced stop input
to servo amplifier
Each
axis
No change
Servo OFF
Servo OFF or free run (The operation stops with dynamic brake)
Fatal stop
(Stop group 1)
Hardware stroke
limit upper/lower
limit error
occurrence
Each
axis
No change During error
Deceleration stop/sudden stop
(Select with "
Pr.37
Sudden stop group 1 sudden stop
selection".)
Deceleration
stop
Error occurs in PLC
CPU
No change
PLC READY signal
OFF
Turns OFF
Emergency stop
(Stop group 2)
Error in test mode
All axes
No change
During error
Delegation stop/sudden stop
(Select with "
Pr.38
Sudden stop group 2 sudden stop
selection".)
Deceleration
stop
Axis error detection
(Error other than
stop group 1 or 2)
Relatively safe stop
(Stop group 3)
"Stop" input from
peripheral device
Each
axis
No change During error
"Stop signal" ON
from external
device
Intentional stop
(Stop group 3)
"Axis stop signal"
ON from PLC CPU
Each
axis
No change
During stop
(during
standing
by)
Deceleration stop/sudden stop
(Select with "
Pr.39
Sudden stop group 3 sudden stop
selection".)
Deceleration
stop